深穴加工の主な加工方法とマシニングセンタを使用の利点 | マシニングセンタ大解剖
特集記事
深穴加工の主な加工方法とマシニングセンタを使用の利点
公開:2024.11.20 更新:2024.11.20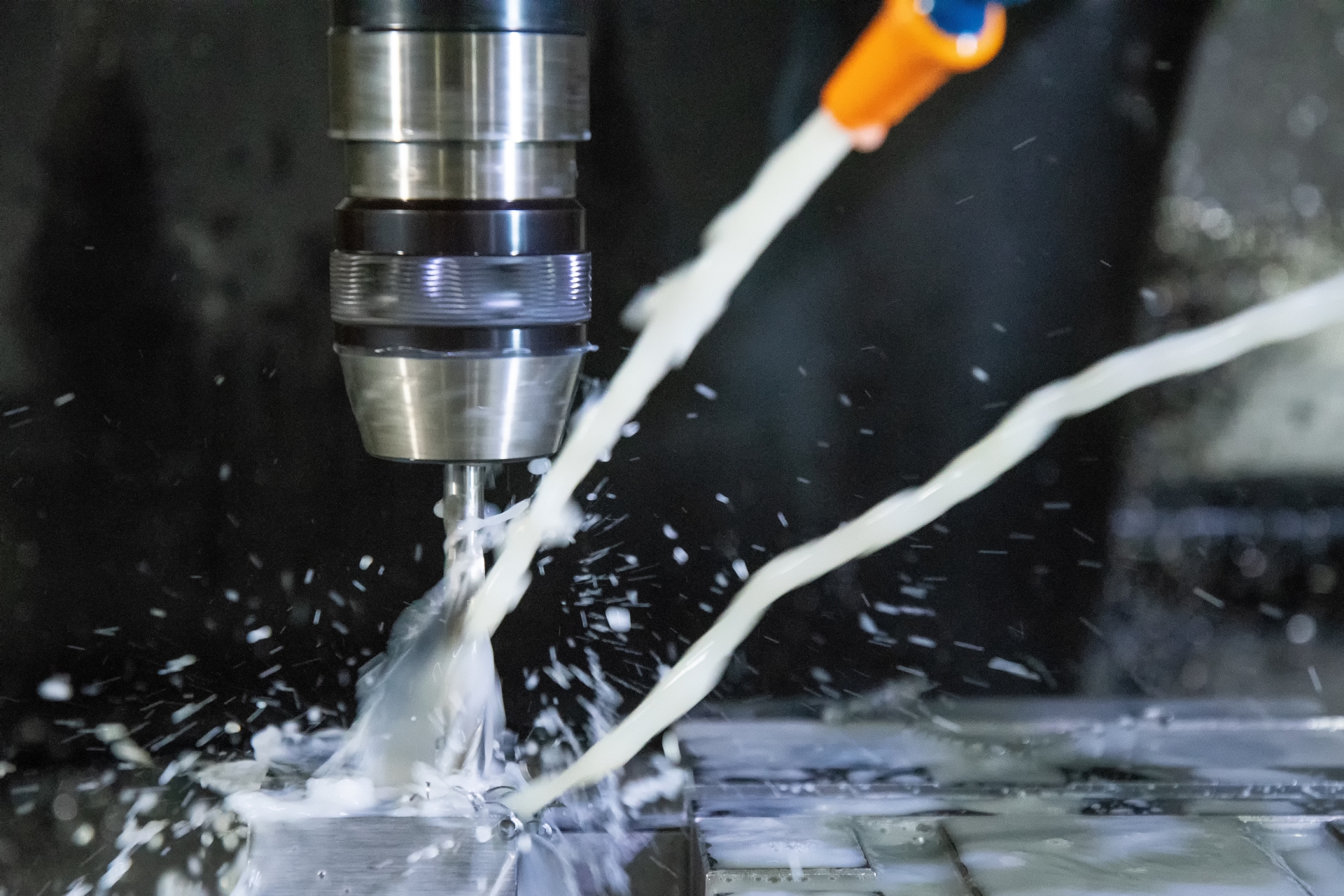
深穴加工は、直径に対して深さが4倍以上の穴を精密に加工する技術で、自動車や航空宇宙、医療機器などの分野で欠かせない役割を果たしています。この加工方法には、ガンドリル加工、BTA加工、放電加工、ロングドリル加工といった複数の手法があり、求められる精度や用途に応じて選ばれます。
近年では、マシニングセンタを利用した深穴加工が注目され、効率的で精度の高い加工が可能となっています。
目次
深穴加工の概要と重要性
深穴加工の進化により、加工可能な素材や形状の幅が広がり、新たな設計や製品開発を可能にしています。深穴加工は、さまざまな製造業で必要不可欠な技術であり、精密で高品質な製品を実現するための重要な技術です。
◇深穴加工とは
深穴加工は、直径に対して深さが4倍以上の穴を加工する技術です。この加工方法は、通常のドリルでは難しい精度や直進性を求められます。深穴加工は、金属や合金をはじめ、さまざまな素材に適用でき、シリンダーやシャフト、金型などを作る際には欠かせない技術です。
深穴加工にはいくつかの手法があります。例えば、ガンドリル加工、BTA加工、放電加工などがあり、それぞれの手法は加工する素材や求められる精度によって選ばれます。ガンドリル加工は細い穴を深く掘るのに向いており、BTA加工はより大きな穴を加工するのに使用されます。放電加工は、非常に精密な穴を開けるための方法です。
この技術は、製造業にとって非常に重要で、精度を確保しつつ、生産効率を高め、コスト削減にも寄与します。深穴加工の適切な選択と実施は、製造の品質や納期に大きく影響します。
◇広く使用される技術
深穴加工は、自動車産業、航空宇宙産業、医療機器製造、石油・ガス産業など、多岐にわたる業界で広く使用されています。例えば、自動車エンジン部品では、燃料噴射装置やオイル通路などの精密な穴加工が必要不可欠です。
航空機では、軽量化と強度の両立が求められる部品の加工に深穴加工が利用されます。
医療分野では、手術器具やインプラントなどの高精度な製品の製造にも欠かせません。また、石油やガス産業では、掘削装置やパイプライン部品の耐久性や安全性を確保するために利用されています。
深穴加工技術は製品の品質向上だけでなく、安全性や性能を支える重要な役割を果たしています。深穴加工技術の普及は、製造業全体の競争力を高める要因となっており、今後も需要が増加すると期待されています。
深穴加工を実現するための主な加工方法
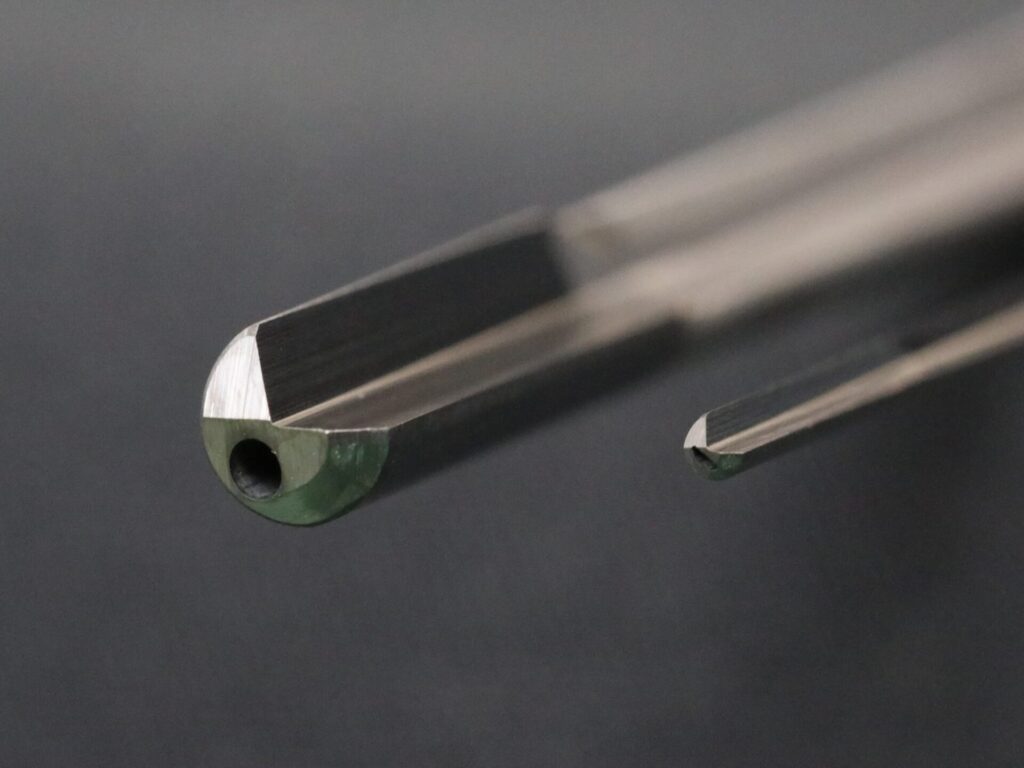
画像出典:佐渡精密株式会社
深穴加工を実現するためには、加工対象や目的に応じて適切な加工方法を選択することが重要です。深穴加工を実現するための主な加工方法は4つあります。各加工方法は、それぞれ特有のメリットを持ち、加工する素材や穴の形状に応じて使い分けられています。
◇ガンドリル加工
ガンドリル加工は、細長い穴を高精度で加工するために開発された技術で、工具の内部に冷却液を供給しながら切削を行うのが特徴です。冷却液は切削時の熱を除去し、切りくずを効率的に排出する役割を果たします。
ガンドリル加工は、特に直径が小さく、長さが深い穴を加工する際に効果を発揮します。ガンドリル加工は、航空宇宙や自動車産業において、燃料噴射ノズルや油圧部品などの製造で広く利用されています。
高い加工精度と滑らかな表面仕上げを実現できるため、精密な穴加工を求められる製品に最適です。
◇BTA加工
BTA加工(ボーリング・トレパン・アソシエーション加工)は、ガンドリル加工と同様に内部冷却を利用する技術ですが、大径の穴を効率的に加工するのに適しています。BTA加工では、工具の外部から冷却液を供給し、内部に切りくずを排出する仕組みが採用されています。
内部に切りくずを排出できるため、大量の切りくず処理が必要な深穴加工においても安定した加工が可能です。BTA加工は、大型のシリンダーや油圧機器の製造で活用され、特に重工業分野で重要な役割を果たしています。
◇放電加工
放電加工は、電極と加工対象物の間で発生する放電によって金属を溶融・蒸発させて穴を加工する方法です。放電加工は、切削加工では困難な硬質材料や複雑な形状の加工に適しています。
また、放電加工は、工具の摩耗が少ないため、極めて高い精度が求められる医療機器や半導体製造装置の部品加工にも利用されており、加工時にほとんど力が加わらないため、脆性材料の加工に最適です。
◇ロングドリル加工
ロングドリル加工は、長尺のドリルを用いて深穴を加工する方法で、比較的シンプルな技術ながら幅広い用途で利用されていますロングドリル加工では、ドリルの剛性と振動を制御することで加工精度を確保します。
また、ロングドリル加工は、中小規模の深穴加工に適しており、自動車部品や建設機械の製造で頻繁に活用され、特殊な工具を組み合わせることで、コストを抑えながら効率的な加工が可能です。
それぞれの方法の課題点
深穴加工を実現するための各加工方法には、それぞれ独自の利点がある一方で、課題やデメリットも存在します。
◇BTA加工・ガンドリル加工の課題
BTA加工とガンドリル加工は、深穴加工の中でも高い精度と効率性を持つ方法ですが、いくつかの課題があります。まず、どちらの方法も専用の高価な機械設備が必要である点が挙げられます。
高価な機械設備の導入が必要なため、初期投資が大きくなるため、小規模な加工や低予算での運用には適しません。また、工具や設備のメンテナンスコストも高く、長期間の運用には定期的な調整や部品交換が求められます。
さらに、加工中の冷却液管理も重要な課題です。冷却液の供給や循環システムが適切に機能しない場合、加工精度の低下や工具寿命の短縮、さらには加工物の不良が発生するリスクがあります。
◇放電加工の課題
放電加工は、硬質材料や複雑な形状に対応できる高精度な加工技術ですが、加工速度が遅いという大きなデメリットがあります。加工速度が遅いため、量産品や大型部品の加工には不向きであり、コスト効率が低下する可能性があります。
また、加工には高電力が必要であり、エネルギーコストがかかる点も課題です。さらに、加工過程で発生する放電によって工具電極が消耗し、頻繁な交換や調整をしなければなりません。
さらに、加工中には熱が発生し、加工物が熱変形するリスクがあるため、温度管理も欠かせません。
◇ロングドリル加工の課題
ロングドリル加工は、比較的シンプルな技術で幅広い用途に対応しますが、加工精度の確保が課題となることがあります。特に、ドリルの剛性が不十分な場合、振動や偏心が発生し、加工面の品質や穴の直進性が損なわれることがあります。
さらに、長いドリルを使用するため、切りくずの排出が難しくなることがあります。切りくずが加工穴内に詰まると、加工が停止したり、ドリルの破損が破損したりする可能性が高いです。
ドリルの破損を防ぐために、冷却液の供給や切りくず排出のシステム設計が重要ですが、その管理には手間がかかることが課題です。
マシニングセンタで深穴加工は可能?課題と解決策
マシニングセンタは、複雑な加工を高精度で行うことができる優れた機械ですが、深穴加工に関しては特有の課題も存在します。ここで、マシニングセンタで深穴加工を行う際の課題と解決策について解説します。
◇マシニングセンタによる深穴加工の課題
マシニングセンタは多機能な工作機械として幅広い加工に利用されていますが、深穴加工においては特有の課題が存在します。マシニングセンタによる深穴加工では、切り屑の排出、冷却や潤滑の不足、工具の剛性不足や振動による加工精度の低下といった問題が発生します。
深穴加工では加工中に大量の切り屑が発生しますが、これを穴の奥からスムーズに排出することが難しく、切り屑が穴内に詰まると工具の破損や加工精度の悪化を引き起こします。
また、穴の深さが増すにつれて冷却液や潤滑油が十分に行き渡らず、工具の寿命を縮めるほか、加工面の品質低下を招く可能性もあります。
さらに、長い工具を使用する深穴加工では工具の剛性が不足しがちで、振動が発生すると直進性や精度が損なわれるリスクがあります。
◇マシニングセンタ用ガンドリル
マシニングセンタでの深穴加工の課題を克服する手段として、マシニングセンタ用ガンドリルが開発されています。マシニングセンタ用ガンドリルは、工具内部に冷却液を供給する機構を備えており、切り屑を効率的に排出すると同時に、工具を適切に冷却・潤滑することが可能です。
工具を適切に冷却・潤滑することにより加工中の熱による工具摩耗を抑え、精度の高い加工を実現します。また、工具の剛性が高く設計されており、振動を抑制することで直進性を確保します。
このような特性により、マシニングセンタでも深穴加工が可能となり、従来の課題が大幅に改善されています。さらに、近年ではガンドリルの性能が一層向上し、マシニングセンタでの深穴加工に特化した製品が登場しています。
深穴加工は、直径に対して深さが4倍以上の穴を高精度で加工する技術で、自動車や航空宇宙、医療機器など多くの産業で重要な役割を果たしています。主な加工方法としてガンドリル加工、BTA加工、放電加工、ロングドリル加工があり、各方法は精度や素材に応じて選ばれますが、それぞれに課題も存在します。
特に、BTA加工やガンドリル加工は高価な設備が必要で、冷却液の管理が重要です。放電加工は精度が高いものの、速度が遅くコストがかかる点がデメリットです。
マシニングセンタでの深穴加工は、工具の剛性不足や冷却の課題を抱えていますが、ガンドリルを用いることでこれらの課題を解決し、精度を保ちながら効率的な加工が可能になっています。深穴加工技術の進化は製造業の品質向上と生産性向上に貢献し、今後ますます重要性を増すと考えられます。
自社にピッタリなマシニングセンタはどれ?
ニーズで選ぶ! おすすめ企業3選
コスト削減とサポート
メクトロン
個別カスタム得意!
充実のアフターサポートも◎
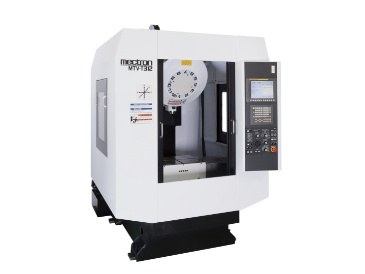
特徴
- ターンキーソリューション対応!設定の手間が省け、失敗のリスクも減らせる
- 自動化システム導入可能!生産性の向上とコスト削減に大貢献
- コンパクトなサイズで設置スペースが限られる工場や作業現場にも適応
品質と耐久性
静岡鐵工所
熟練の技で一台一台を
丹念につくり込む
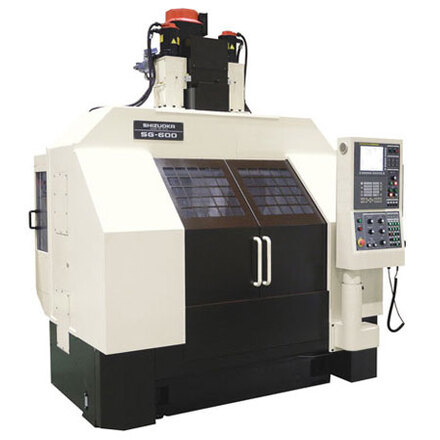
特徴
- 熟練した職人の手で施される、精密かつ耐久性の高い製品
- 強力なギヤヘッドを搭載し、幅広い加工に対応可能

メディア推奨 メーカー6選

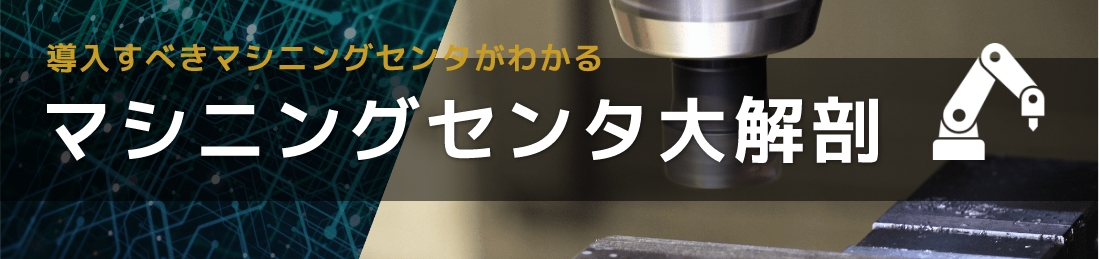