マシニングセンタの精度を左右する要因と精度向上に成功した事例 | マシニングセンタ大解剖
特集記事
マシニングセンタの精度を左右する要因と精度向上に成功した事例
公開:2024.06.28 更新:2025.03.03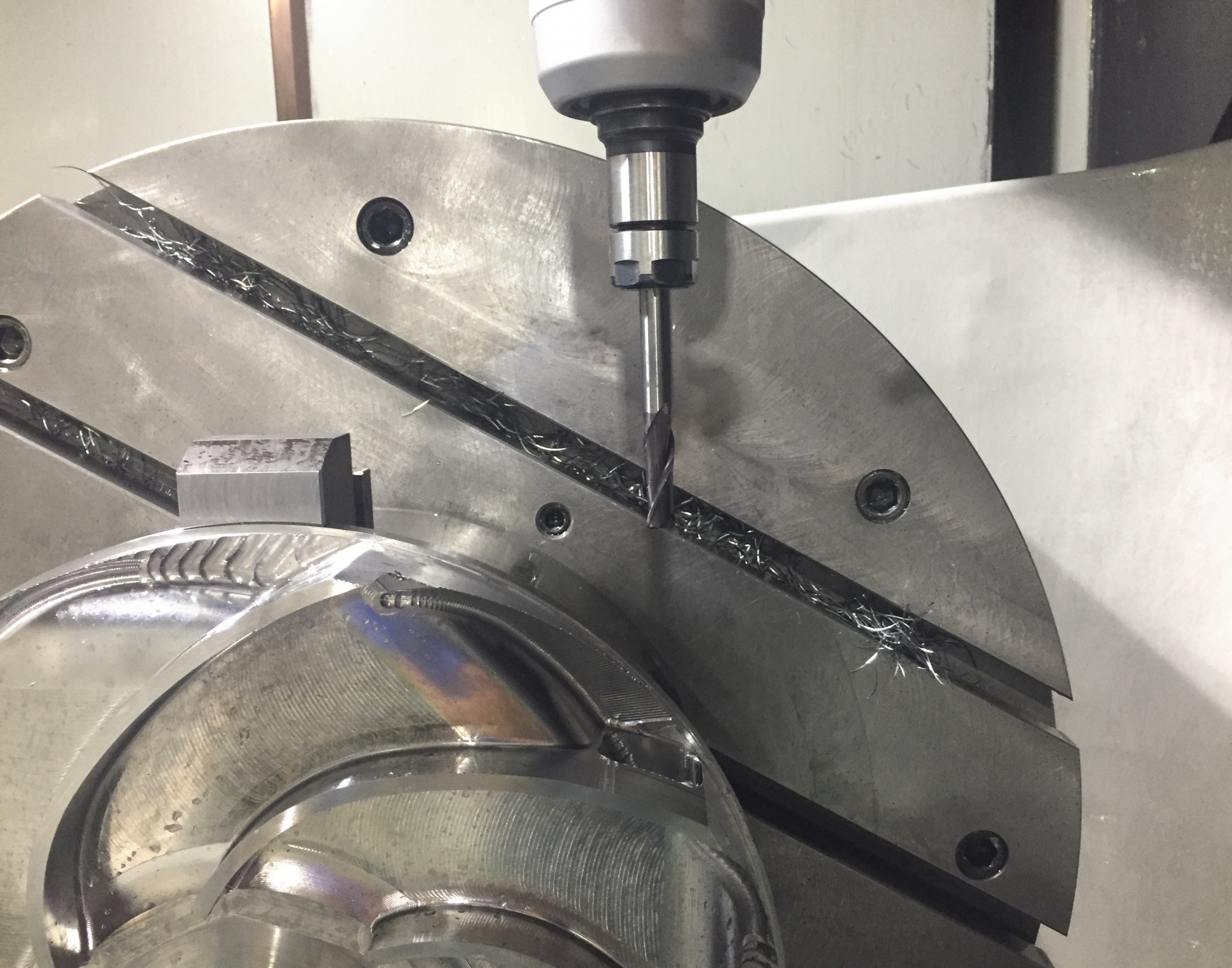
マシニングセンタは、高精度な加工が可能な工作機械として広く利用されていますが、その精度を左右する要因は様々です。マシニングセンタの精度を最大限に引き出すためには、事前準備やメンテナンス、加工方法の選択など、様々な要素を考慮する必要があります。
こちらでは、マシニングセンタの精度を左右する要因について詳しく解説し、実際に精度向上に成功した事例をご紹介します。
目次
加工精度とは?マシニングセンタの精度について
加工精度は製造業において重要な概念です。これは、加工された部品や製品が設計通りの寸法や形状精度、表面仕上げ、角度・傾斜の精度をどれだけ正確に再現できるかを示す指標です。特にマシニングセンタの場合、CADやCAMで設計した通りに動作し、高精度な加工を実現します。
◇ 加工精度とは
加工精度とは、加工後の製品が設計図通りに作られているかどうかを表す尺度です。具体的には、寸法精度、形状精度、表面仕上げ、角度・傾斜精度などの精度をさします。
切削加工における加工精度は、部品や製品の正確な寸法や形状を保つために極めて重要です。加工精度が低いと、設計通りの性能や機能が発揮されず、製品の品質や信頼性が低下する可能性があります。
寸法精度や形状精度、表面仕上げ、角度・傾斜の精度は、設計図面で指定された寸法公差や許容差内で加工されることが基本です。一般的に、公差は「±Xmm」または「±Xμm」で表され、たとえば「±0.05mm」は、加工された部品の寸法が設計から±0.05mmの範囲内で許容されることを意味します。
◇ マシニングセンタの精度
マシニングセンタは、その高い加工精度によって多くの製造現場で重宝されています。CADやCAMで作成した設計通りに動作するため、高精度な加工が可能です。これにより、従業員の技術力に左右されずに一貫して品質の高い製品が生産できます。
また、個体差が小さく安定した品質を保つことができ、品質の安定化とともに手直しの手間も大幅に削減できます。これにより、付加価値の高い業務に集中できるだけでなく、労力を低減してプログラム作成などの作業に注力することが可能です。
マシニングセンタの精度の現状
マシニングセンタは高精度な加工ができるため、多くの製造現場で利用されています。しかし、どんなに高精度であっても、問題が全くないわけではありません。ここでは、マシニングセンタの精度に関する現状を説明します。
◇ テーブルの送り速度
マシニングセンタの中には、F1,000やF3,000を超える優れたテーブルの送り速度を持つ機種もあります。しかし、最高速度を設定すれば必ずしも加工が速くて良くなるわけではありません。
例えば、狭い溝や穴の内側を加工する際、短距離での方向転換が多くなります。このような場合、最高速度ではうまく対応できないことがあります。最新のマシニングセンタでは、プログラムを先読みして送り速度を自動で調整する機能がありますが、そうでない機種では、機械に揺れやぶれが生じる可能性があります。
高精度で仕上げたい場合は、単に最高速度を設定するのではなく、加工エリアに応じて速度を調整することが重要です。短距離で方向転換が多い場合は低速、十分な長距離があれば高速と、パスを使い分けることが必要です。
◇ 端面基準
マシニングセンタは高精度な加工が可能ですが、誤差が全くないわけではありません。特に金属などの硬い材料を加工する際には、工具が少し逃げて0.01〜0.03ミリ程度の誤差が発生することがあります。工具径補正機能を活用すれば、ある程度は誤差を補正できますが、誤差が存在することは理解しておく必要があります。
誤差を無視すると、再加工の際に誤った基準で位置決めをしてしまうことがあります。例えば、単純に端面基準でX原点を決めるような判断をしてしまうと、最初の加工で生じた誤差が再加工でさらに大きくなってしまいます。再加工を行う場合は、誤差を軽視せず、実際に測定した値を基に基準を決め、入力内容を調整することが重要です。
マシニングセンタの精度を上げる為に大切なこと
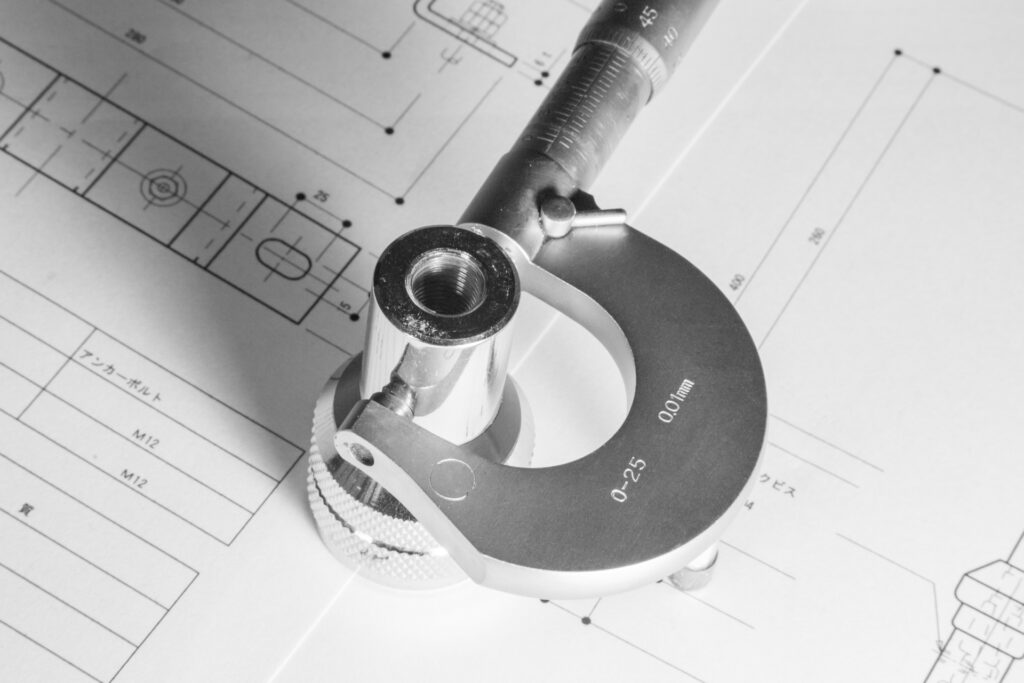
画像出典:フォトAC
マシニングセンタは、高い精度で加工できる汎用性の高い工作機械です。しかし、精度を最大限に引き出すためには、適切な設定やメンテナンス、加工方法の選択など、様々な要素を考慮する必要があります。
◇ 事前準備
マシニングセンタで作品の精度を高めるためには、事前準備が不可欠です。まず、マシンの状態を整えることが重要です。定期的なマシンの掃除や部品交換を行うことで、正確な作業が可能になります。特に切削工具の定期チェックは欠かせません。
また、加工前の金属材料を正確な寸法に加工し、材質や要求精度に応じた切削工具や加工治具を選定することも重要です。さらに、切削条件の設定(切削速度、送り速度、切削深さ、切削方向)を適切に行うことで、精度を確保し、工具の寿命も延ばすことができます。
◇ 工具のメンテナンス
高品質な工具を選ぶことは基本ですが、それだけでは十分ではありません。定期的なメンテナンスを行うことで、工具の摩耗や欠陥を最小限に抑えることができます。具体的には、定期的な清掃やオイルやグリスの交換を行い、切削工具の寿命を延ばします。また、必要に応じて研削や研磨を行い、切れ味を保つことも重要です。
◇ 適切なプログラムの作成
適切なCAD/CAMプログラムの作成も重要です。CAD(Computer Aided Design)で設計された図面を元に、CAM(Computer Aided Manufacturing)ソフトウェアが加工プログラムを生成し、マシンがその通りに動作します。
ソフトウェアが加工現場のニーズに適合し、使いやすいインターフェースを持つかどうか、サポート体制がしっかりしているかなどを考慮する必要があります。適切なソフトウェアの導入は、加工の品質向上に直結し、生産性を高めるための重要なステップです。
確認不足や工具の不良により精度不足となる場合も
製造業において、工具の不良やメンテナンス不足は、製品の品質に直接影響を及ぼす重要な問題です。これらの問題が原因で、製品の精度が低下し、最終的には顧客の信頼を失うことにも繋がりかねません。
ここでは、工具の不良とメンテナンス不足がどのように精度不足を引き起こすのか、具体的な例を挙げて解説します。
◇工具の不良による精度不足
バイスは、工作機械において材料を固定するために使用される工具です。バイスの精度が不十分であると、加工される材料が適切に固定されず、結果として加工誤差が生じる可能性があります。
例えば、バイスの口が平行でない場合や、摩耗によってガタが生じている場合などが挙げられます。これらの問題は、加工中に材料が動いてしまい、寸法や形状が設計通りにならない原因となります。
◇メンテナンス不足
テーブル軸線が理想的にはY軸と平行であるべきですが、実際にはX軸周りやZ軸周りにわずかな傾きが生じることがあります。この傾きが大きくなると、加工精度に問題が生じる可能性があります。
実際の事例では、立て形マシニングセンターのテーブル上面が0.2ミリも傾いていることが判明しました。この傾きは、メンテナンス不足により水平器での定期的な確認が怠られていたことに起因しています。
このような事例からも、マシンの精度維持において定期的なメンテナンスが重要であることが分かります。
5軸制御立て形マシニングセンタの導入で精度向上に成功した事例
製造業においては、高精度な部品の製作がますます求められています。従来の3軸制御マシニングセンタでは加工が難しかった複雑な形状や、高精度な部品の製作には、5軸制御立て形マシニングセンタが有効です。
今回ご紹介する事例は、5軸制御立て形マシニングセンタ導入によって、加工精度を大幅に向上させた企業の成功事例です。
◇ 導入の経緯
研究開発の現場では、高精度な部品の製作が求められる場面が多くありますが、従来の3軸制御の立て形マシニングセンタではいくつかの重要な課題が浮き彫りになっていました。まず第一に、難削材や高精度な部品の短納期納入が非常に難しく、試作品を製作するためには多くの時間がかかることが頻繁にありました。これにより、製作スケジュールの遅れやプロジェクト全体の進行に支障をきたすことがありました。
また、部品形状に応じて段取り替え治具を製作する必要があり、その作業にも時間を要しました。治具の製作には専門的な技術と時間が必要であり、その分生産性が制限され、効率的な加工が行えないことが課題となっていました。さらに、加工中に求められる厳しい表面粗さの要求を満たすためには、通常、2段階方式で仕上げ加工を行わなければならず、これが加工時間の延長やコストの増加を引き起こす要因となっていました。
これらの課題を解決するため、5軸制御立て形マシニングセンタの導入が決定されました。5軸制御マシニングセンタは、従来の3軸制御機に比べて圧倒的に多機能であり、複雑な形状や多角度からの加工が可能です。これにより、従来のように段取り替え治具を多く必要とすることなく、部品を一度のセットで加工できるため、生産性が大幅に向上しました。また、5軸制御により精密な加工が可能となり、高精度な部品の製作が短期間で行えるようになりました。
特に、5軸制御マシンは、複雑な部品形状を一度の加工で仕上げることができるため、2段階方式での仕上げ加工を必要とせず、加工時間やコストの削減が実現できます。これにより、研究開発現場において求められる短納期と高精度が両立し、効率的かつ迅速に部品を製作できるようになりました。このようなマシニングセンタの導入により、研究開発の効率化と製品の品質向上が達成されました。
◇ 時間短縮と精度向上を実現
5軸制御立て形マシニングセンタの導入により、段取り替えや治具製作の負担が大幅に軽減されました。特に、5軸制御による多角度からの自在な加工が可能になったことで、ワンチャッキングで複雑な部品の大部分を1台で加工できるようになりました。
また、5軸加工機の「ファイブチューニング」機能により、朝一での調整で幾何段差や芯ずれを自動補正し、1回の調整で段差のない高精度な加工が実現できるようになりました。
これにより、製造プロセス全体の効率が向上し、納期の短縮や品質の向上に大きく貢献しています。
マシニングセンタを取り扱っている企業を紹介
製造業では、5軸制御立て形マシニングセンタを含む高精度な製品が求められています。以下に、高精度なマシニングセンタを提供している代表的な企業を6社紹介します。
◇メクトロン
工場の自動化に強みを持ち、小型マシニングセンタに力を入れたメーカーです。1929年に鉄工用ヤスリの製造からスタートし、1964年から工作機械用ツールの生産を開始。現在はさまざまなマシニングセンタを開発しています。特にMTV-T331wは5軸制御でコンパクトな設計、5面加工が可能で、高速主軸で効率的な仕上がりが期待できます。
また、メクトロンはマガジンダイレクトATCやダブルアームATCなど、ツール交換の方式にも特徴があり、効率的な加工を支援しています。
◇松浦機械製作所
5軸マシニングセンタを主力とするグローバル企業で、1935年に旋盤メーカーとして創業、1974年からマシニングセンタを取り扱っています。松浦機械製作所の製品は、リーズナブルで扱いやすいシリーズから自動化・無人化が可能なシリーズまで幅広く提供されています。
特にMAM72シリーズは、同時5軸制御により複雑な加工と自動化・無人化を両立させ、最大60個のパレットチェンジャを選択可能です。多品種少量生産に適しており、さまざまな企業から注目を集めています。
◇大鳥機工
1948年に繊維機械メーカーとして設立され、1986年からマシニングセンタの製造を開始。大鳥機工は、旋削機能付きの5軸制御立て形マシニングセンタに強みを持ち、特にFTV-500iHVはターニング機能を備えており、小さな丸い部品の旋削加工が可能です。
大鳥機工の製品は、旋削機能付きの5軸マシニングセンタを中心に、さまざまなスタイルで提供されています。特にこのターニング機能付きのマシニングセンタは、精密な加工が求められる分野で注目を集めています。
◇安田工業
0.001㎜の加工精度を誇り、国内最高峰の精度で知られるメーカーです。安田工業は1929年に商会として創業し、1966年からマシニングセンタの開発を始めました。安田工業は、精度を最重要視した経営活動を行い、その高精度のマシニングセンタは国内外で高く評価されています。
特に、フェラーリ社のエンジン部品加工にも採用されるなど、精度の高さで注目されています。安田工業の製品は、キサゲ加工や姿勢変化の少なさに強みを持ち、立て形・横型・5軸・微細など、幅広いシリーズを取り扱っています。
◇三井精機工業
1928年に精密工作機械メーカーとして創業し、1970年からマシニングセンタの生産を開始。三井精機工業は、金型加工や航空宇宙分野で多くの実績を持つ高精度な工作機械を提供しています。
特に5軸マシニングセンタに強みを持ち、ジェイムズウェッブ宇宙望遠鏡のベリリウム製主鏡の加工には、三井精機工業の横形マシニングセンタAS6Aが使用されました。三井精機工業は、高精度と信頼性を誇り、航空宇宙分野や金型加工など、精密な加工が求められる分野で高い評価を得ています。
◇牧野フライス製作所
高精度・高速なマシニングセンタを手掛け、国内4位の大手工作機械メーカーです。牧野フライス製作所は1937年にフライス盤専門メーカーとして創業し、1966年に国内初のマシニングセンタを開発しました。
牧野フライス製作所は、金型加工や航空宇宙、医療機器分野の実績も豊富で、特に横形マシニングセンタの製造や高速かつ高精度な主軸に強みを持っています。また、牧野フライス製作所の5軸マシニングセンタD500は、国立天文台にも採用されるなど、その高性能が証明されています。
◇オークマ
最新技術を積極的に導入する工作機械メーカーで、国内トップシェアを誇ります。オークマは1898年に製麺機メーカーとして創業し、1968年からマシニングセンタの製造を開始しました。
オークマは、精度や剛性、熱変位補正技術において高い評価を得ており、特に5軸マシニングセンタや複合加工機に強みを持っています。オークマの製品は、精度や剛性に優れ、精密な加工が求められる業界で広く使用されています。また、オークマの技術は、世界中で評価されており、グローバルに展開しています。
加工精度は製造業において至上の重要性を持ちます。加工精度には寸法精度、形状精度、表面仕上げ、角度・傾斜精度などが含まれ、これらが公差内で達成されることが基本です。
マシニングセンタはCAD/CAMにより設計通りに動作し、高精度な加工を実現します。これにより品質の一貫性が確保され、手直しの必要性が低減されます。しかし、精度を最大化するには適切な設定、定期的なメンテナンス、適切な切削条件の設定が不可欠です。
工具の不良やメンテナンス不足は加工精度に直結し、正確な加工を妨げる要因となりますので、定期的な管理が欠かせません。5軸制御立て形マシニングセンタの導入事例では、複雑な形状や高精度部品の製作が効率的に行われ、生産性と品質の両面で大きな改善が見られました。
自社にピッタリなマシニングセンタはどれ?
ニーズで選ぶ! おすすめ企業3選
コスト削減とサポート
メクトロン
個別カスタム得意!
充実のアフターサポートも◎
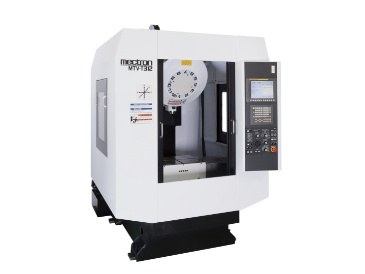
特徴
- ターンキーソリューション対応!設定の手間が省け、失敗のリスクも減らせる
- 自動化システム導入可能!生産性の向上とコスト削減に大貢献
- コンパクトなサイズで設置スペースが限られる工場や作業現場にも適応
品質と耐久性
静岡鐵工所
熟練の技で一台一台を
丹念につくり込む
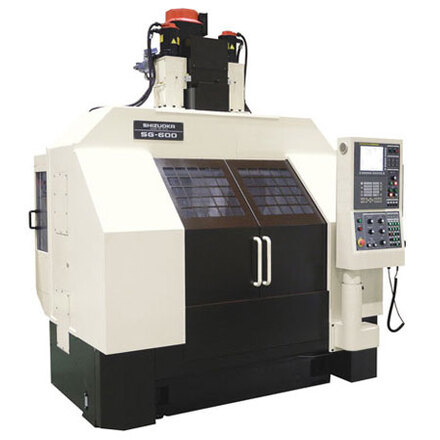
特徴
- 熟練した職人の手で施される、精密かつ耐久性の高い製品
- 強力なギヤヘッドを搭載し、幅広い加工に対応可能

メディア推奨 メーカー6選

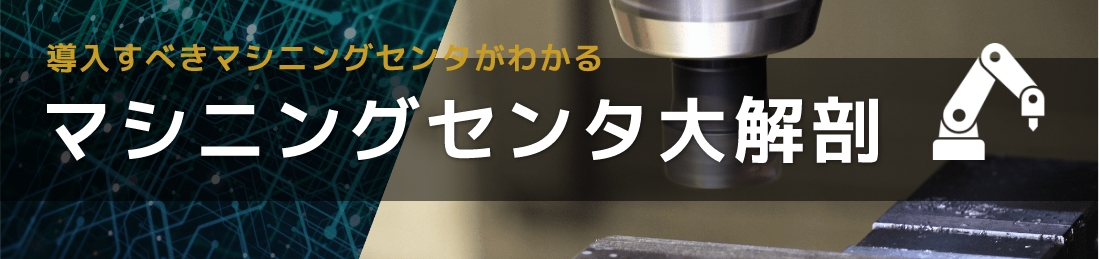