硬すぎて削れない?マシニングセンタによる難削材加工の難しさと必要条件 | マシニングセンタ大解剖
特集記事
硬すぎて削れない?マシニングセンタによる難削材加工の難しさと必要条件
公開:2024.06.26 更新:2024.12.25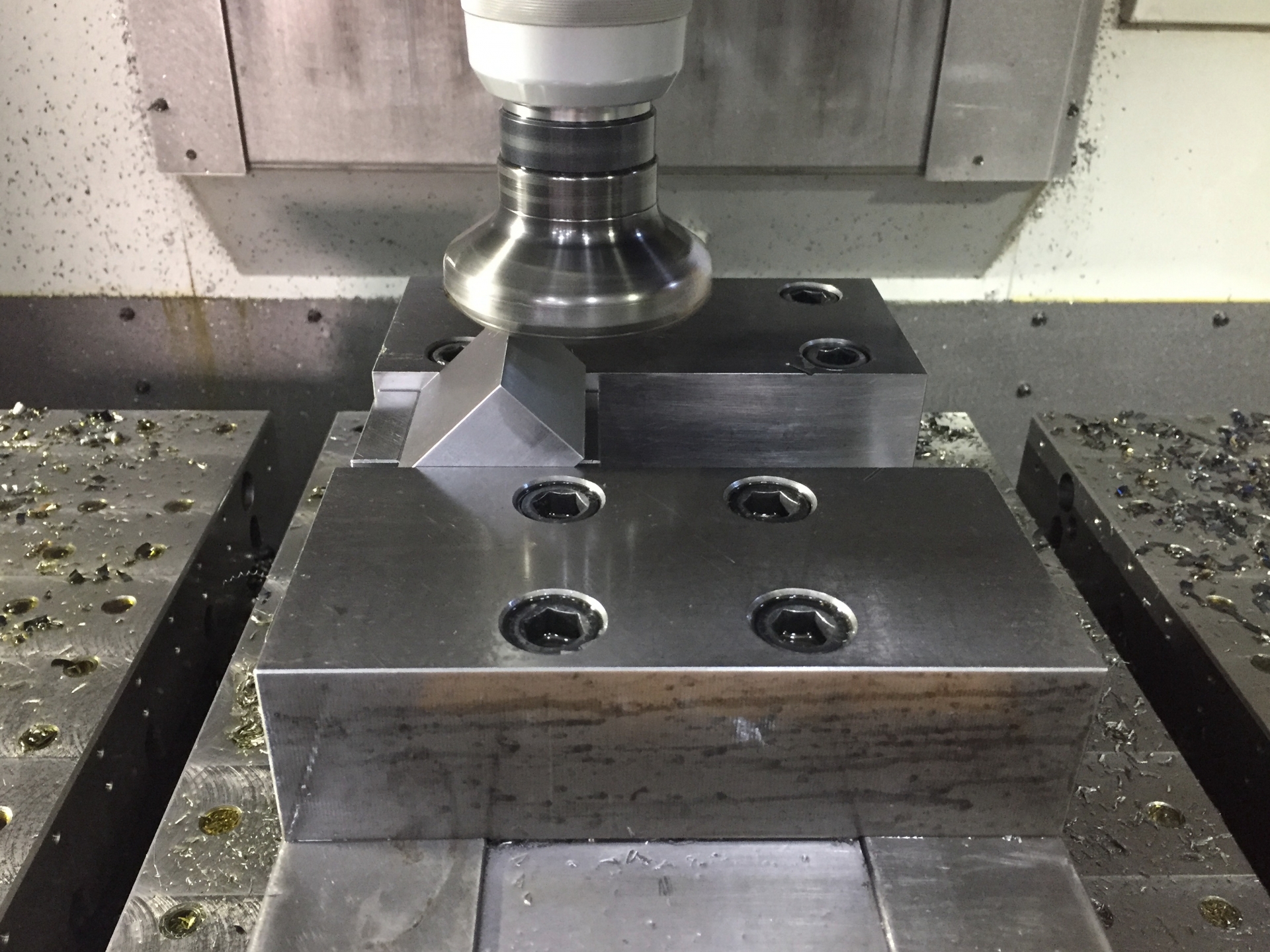
難削材の加工は、その硬度や特性ゆえに、一般的な加工方法では容易ではありません。特にマシニングセンタを用いた加工では、適切な工具と切削条件の選定が不可欠です。
例えば、超耐熱合金やインコネルなどの材料は、高温や腐食に強い反面、その硬さから工具の摩耗や切り屑の管理が難しく、加工過程での精度維持が難しい課題があります。こちらでは、難削材の特性ごとの種類や加工を行うために必要なことについて詳しく解説します。
目次
難削材を加工する目的と特性別の種類
難削材とは、一般的な加工方法では容易に形を変えることができない素材のことを指します。これらの材料は、高い耐久性や耐熱性を持ち合わせており、航空宇宙産業や医療機器など、特定の高性能を要求される分野での使用が目的です。
マシニングセンタなどの先進的な加工技術を用いることで、これらの難削材も精密に加工することが可能となります。
◇ 難削材とは
難削材とは、加工や取り扱いが難しい材料のことを指します。難削材にはいくつかの種類があり、それぞれの素材特性によって加工設備や加工条件、切削工具に与える影響が大きく異なります。
例えば、耐摩耗性、耐熱性、耐食性などの特性を持つ難削材は、製品の高機能化や高品質化に不可欠な材料です。しかし、これらの特性があるために、加工が難しくなるのです。
つまり、難削材は高い性能を持ちながらも、その加工には高度な技術と適切な設備が必要です。そのため、難削材の加工を成功させるためには、素材に応じた専門的な知識と経験が求められます。
◇ 特性別の種類
難削材にはさまざまな種類があり、それぞれ特有の性質を持っています。以下で、主な難削材の種類とその特性について解説します。
まず、硬度が高い材料には、超耐熱合金、チタン合金、ステンレスなどがあります。これらは、切削抵抗が大きくなり、工具摩耗が早くなります。
次に、熱伝導率が低い材料には、高硬度鋼(焼入鋼、ダイス鋼、高速度工具鋼、プリハードン鋼)やコバルト基超耐熱合金(ステライトなど)があります。これらの材料は熱を効率的に逃がすことができず、切削中に熱が工具に集中してしまいます。
また、加工硬化性が高い材料には、インコネル、ハステロイ、ワスパロイ、耐熱鋼、高マンガン鋼などがあります。これらの材料は加工中に硬さが増す性質があり、このため工具の刃先が欠けやすくなります。
さらに、工具材種との親和性が大きい材料には、純チタン、ステンレス鋼、チタン合金、超耐熱鋼などがあります。これらの材料は切削抵抗が大きいため、工具にかかる負荷が高くなります。切削抵抗が大きいことで、工具の摩耗や損傷が発生しやすくなります。
最後に、熱膨張率が大きい材料にはステンレス鋼があります。この材料は切削中に熱を受けると膨張しやすくなります。
代表的な難削材を紹介
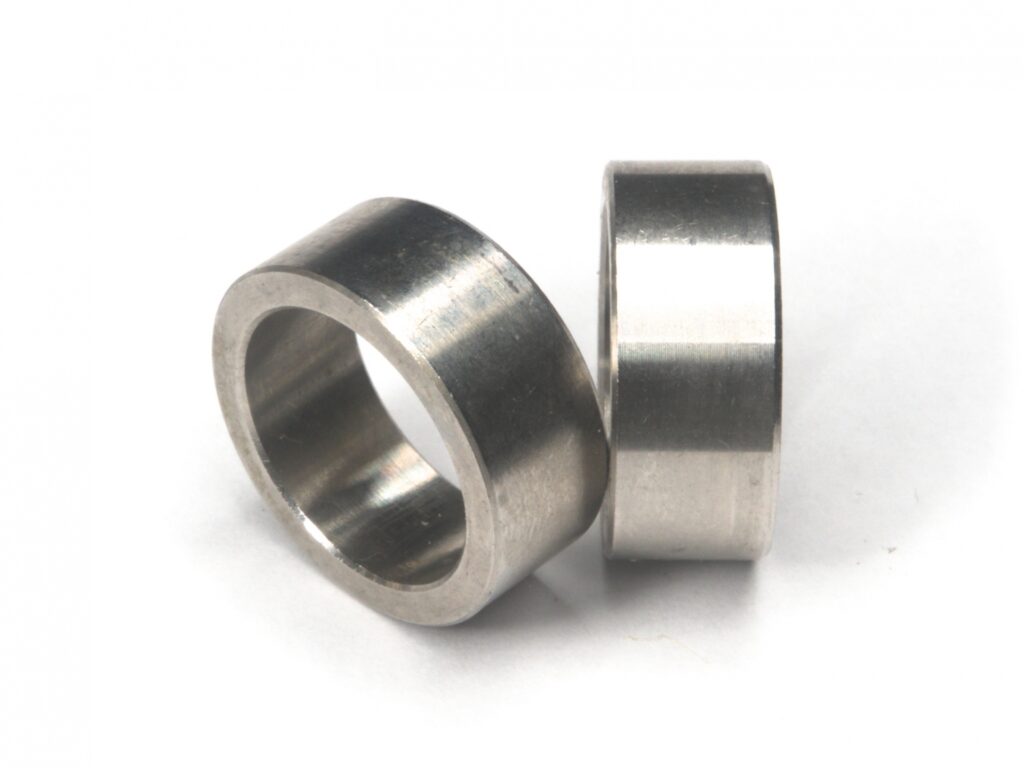
画像出典:フォトAC
難削材はその特性から加工が困難であり、特別な技術や機械が必要とされます。ここでは、代表的な難削材であるステンレス、チタン、インコネルについて、それぞれの特性や用途を詳しく解説します。
◇ステンレス
ステンレスは、耐食性と耐熱性に優れた合金で、その名の通り「錆びにくい」という特性を持っています。これは、クロムやニッケルなどの元素を含むことにより、表面に酸化クロムの保護膜を形成し、錆や腐食を防ぐためです。ステンレスは、キッチン用品や医療器具、建築材料など、幅広い分野で利用されています。
◇チタン
チタンは、軽量でありながら強度が高く、耐食性にも優れているため、航空宇宙産業や医療分野で重宝されています。また、人体への親和性が高いことから、人工関節やインプラントなどの生体材料としても使用されています。チタンの加工は難しく、高い切削温度や工具の摩耗が問題となることがあります。
◇インコネル
インコネルは、ニッケルを主成分とする超合金で、極めて高い耐熱性と耐食性を持っています。このため、ジェットエンジンや化学プラントの部品など、高温かつ腐食性の環境下で使用されることが多いです。
インコネルの加工には、高度な技術と特殊な工具が必要であり、その加工コストは非常に高くなります。
これらの難削材は、それぞれ独自の特性を活かして、現代社会の様々な分野で不可欠な役割を果たしています。
◇コンスタンタン
コンスタンタンは、銅とニッケルを主成分とする特殊な合金で、主に熱電対などの温度測定機器に使用される金属です。特に、電気抵抗が温度によってほとんど変化しない特性があり、高精度な温度計測において重宝されています。しかし、コンスタンタンは加工が非常に難しい金属としても知られています。
まず、コンスタンタンは非常に柔らかいため、加工中に強い力を加えると簡単に変形してしまいます。この柔らかさが、マシニングセンタでの加工時に大きな障害となります。具体的には、固定具でのチャッキングが非常に難しく、強すぎると変形し、弱すぎると加工中に位置がずれる可能性があります。そのため、加工精度を保つためには非常に繊細な固定が求められます。
また、切削条件の設定にも慎重さが必要です。切削速度や工具の選定を誤ると、表面仕上がりにムラが出たり、工具の摩耗が早まる可能性があります。コンスタンタンの加工には、経験豊富なオペレーターと高精度な機械が必要不可欠です。
◇マグネシウム
マグネシウムは、非常に軽量で強度が高いという特性を持つ金属で、自動車、航空宇宙産業、電子機器などで広く利用されています。特に、軽量化が求められる製品にとっては不可欠な素材ですが、その一方で加工が難しい金属でもあります。
マグネシウムは柔らかいため、加工中に強い力を加えると変形しやすく、切削加工時には発火のリスクがあるため、安全対策が非常に重要です。マシニングセンタでの加工では、切削条件の設定に細心の注意を払う必要があります。切削速度、送り速度、冷却液の使用など、すべての要素に慎重を期さなければなりません。
さらに、マグネシウムの加工においても固定具でのチャッキングが難しく、強すぎると変形し、弱すぎると加工中に位置がずれる可能性があります。そのため、適切な固定力と安定性を確保するための工夫が求められます。また、切削工具も摩耗が早くなるため、耐摩耗性の高い工具を選ぶことが重要です。
難削材の加工が難しい理由
難削材の加工には多くの挑戦が伴います。これらの材料は、その特性上、加工時に様々な問題を引き起こす可能性があります。以下に、その主な理由を解説します。
◇ 材料の硬度と加工機器への負担
硬度の高い材料は、加工時に強い抵抗を工具に与えます。これは、材料の原子同士が強く結合しているため、切断や除去するのに多くのエネルギーが必要となるからです。また、加工機器全体にも大きな負担がかかります。
特に、工作機械の主軸や送り軸などの回転機構や、工具ホルダなどの保持機構は、強い切削抵抗によって負荷が集中し、摩耗や破損のリスクが高くなります。そのため、適切な加工方法を選定し、場合によっては研磨、切削、研削などの異なる方法を組み合わせることが必要です。
◇ 材料の変形と加工硬化の問題
加工中に材料が変形することは、精密な加工を行う上で大きな障害となります。特に難削材は、加工時に内部の応力が解放されることで変形しやすくなります。これにより、意図した寸法や形状が崩れてしまい、加工精度に悪影響を及ぼすことがあります。
また、加工硬化も重要な問題です。加工硬化とは、金属に力を加えて塑性変形させると、変形した部分が硬くなる現象を指します。この現象が起こると、変形した部分が硬くなるため、次の加工が難しくなります。
硬くなった金属は脆くもなり、切削や削り取りが困難になるだけでなく、破損しやすくもなります。そのため、加工硬化を避けるために、加工方法や条件を慎重に選定する必要があります。
◇ 切り屑の溶着と発火のリスク
切削加工では、切り屑が発生しますが、難削材の場合、これが溶着してしまうリスクがあります。切り屑が工具や加工面に溶着すると、加工精度が低下するだけでなく、工具の破損にもつながります。
また、切削速度が高い場合には、切り屑が発火する危険もあり、これは作業者の安全にも関わる重大な問題です。
◇被削性が不明
難削材の加工が難しい理由の一つに、被削性が不明であることが挙げられます。被削性とは、素材が切削加工に適しているかどうかを示す特性で、切削抵抗や熱伝導率、摩耗特性など、さまざまな要素が影響します。難削材の場合、これらの特性が通常の金属とは異なり、加工中に予期せぬ問題が発生しやすいのが特徴です。
たとえば、難削材は切削中に工具と素材の間で高温が発生しやすく、熱伝導率が低い場合、発生した熱が工具側に集中し、工具の摩耗が早まる原因となります。また、被削性が不明な素材では、切り屑がどのように形成されるか予測しづらく、これが工具や加工対象に悪影響を与えることがあります。さらに、被削性が不明確な素材は、切削速度や送り量、工具材質などの切削条件を設定するのが難しく、試行錯誤が必要になります。
特に新素材や特殊合金の加工では、設計段階での強度や耐久性が重視される一方で、加工のしやすさが考慮されていないことが多いため、加工中にトラブルや生産性の低下が発生し、コストが増加するリスクがあります。
この問題を解決するためには、加工実験やシミュレーションを通じて素材の被削性を事前に把握し、最適な切削条件を見つけ出すことが重要です。また、工具メーカーや加工機械メーカーとの密な連携を通じて、素材に最適な加工方法や技術の開発が求められます。
難削材マシニング加工のポイント
難削材のマシニング加工は、精密かつ効率的な方法で行う必要があります。そのためには、マシニングセンタと保持具の剛性を確保し、最適な切削条件を見極め、適切な切削工具を選定することが重要です。
◇マシニングセンタと保持具の剛性
マシニングセンタと保持具の剛性は、加工精度を保つ上で不可欠です。剛性が高いほど、工具の振動が少なくなり、加工面の仕上がりが向上します。また、剛性が確保されていると、より大きな切削力に耐えることができ、加工効率も上がります。
◇最適な切削条件
切削速度と加工条件の調整は、難削材の加工において特に重要です。切削速度が速すぎると工具の摩耗が早まり、遅すぎると加工時間が長くなります。また、加工条件によっては、工具や材料に過度な熱が発生し、品質に影響を与える可能性があります。
そのため、材料の特性や工具の仕様に合わせて、最適な切削条件を見つけることが求められます。
◇適切な切削工具の選定
難削材の特性には硬度の高さや熱伝導率の低さなどがあります。これに応じて、適切な切削工具を選定することが重要です。例えば、硬度の高い材料には超硬合金やダイヤモンドコーティングされた工具が適しています。
熱伝導率の低い材料にはセラミック工具や特殊コーティング工具が効果的です。加工硬化性が高い材料には剛性が必要な高速鋼工具が適しています。これらの適切な工具選びが、高精度で効率的な加工を実現し、品質の向上に寄与します。
◇機械プログラムの微調整
難削材のマシニング加工では、機械プログラムの微調整が不可欠です。難削材は、通常の金属材料に比べて切削抵抗が高く、熱の発生も多いため、標準的なプログラム設定では加工精度や工具寿命に悪影響を及ぼすことがあります。
機械プログラムを調整するためには、切削速度や送り量の設定を慎重に行う必要があります。これらのパラメータは、工具の摩耗や熱の発生に直結するため、難削材に適した低速・高送りの組み合わせを試行しながら調整します。また、切削深さを適切に設定することで、工具への負荷を均等に分散させ、摩耗を抑えることができます。
さらに、難削材では切り屑処理が加工品質に大きな影響を与えるため、切り屑排出の効率を考慮したプログラム設計が必要です。切削パスを短縮し、加工面を効率的にクリアにすることで、切り屑が加工部位や工具に絡むリスクを減らします。
機械プログラムの微調整では、冷却液の使用方法や切削工具の材質も重要です。冷却液の流量や噴射角度を適切に設定することで、加工熱の影響を抑え、工具寿命を延ばすことができます。また、難削材に適した耐摩耗性の高い工具材質を選択することも、加工効率の向上に繋がります。
◇連続運転しない
難削材のマシニング加工では、連続運転を避けることが非常に重要です。難削材は切削抵抗が高く、加工中に工具や素材に大きな熱が発生しやすいため、熱が蓄積すると工具の摩耗や劣化が早まり、素材の性質にも影響を与えて加工精度が低下します。そのため、加工工程を分割し、適切な休止を挟むことがリスク軽減に繋がります。
連続運転を行うと、工具が高温にさらされ続けて摩耗が進行し、切削性能が低下します。これにより、表面仕上げにムラが生じたり、精密加工が難しくなったりします。また、難削材では熱膨張や応力が発生し、加工寸法に影響を与えることもあります。したがって、加工中に冷却時間を設けることで、工具や素材を適切な温度に保つことが重要です。
加工効率を確保するためには、事前に作業スケジュールを計画し、連続運転を避ける設計を組み込むことが求められます。例えば、加工サイクルを短く分割し、工具交換や冷却時間を組み込むことで、工具寿命を延ばし、加工精度を安定させることが可能です。また、冷却液や空冷システムを活用して、加工中の熱影響を最小限に抑えることも有効です。
難削材の加工では、効率と品質のバランスを取るために、連続運転を避け、適切な休止を取り入れることが重要です。これにより、工具や機械への負荷を軽減し、高精度な加工を維持できます。
マシニングセンタを取り扱っている企業を紹介
国内には多くのマシニングセンタを取り扱う企業が存在しますが、その中でも業界をリードする代表的な企業をいくつかご紹介します。それぞれが独自の技術や製品を通じて、多様な産業の発展に貢献しており、国内外で高い評価を受けています。
◇メクトロン
メクトロン株式会社は、フレキシブルプリント配線板(FPC)の製造を中心に事業を展開しています。特に、多層構造や高密度設計のFPCを提供しており、スマートフォンや自動車部品、医療機器など、さまざまな分野で使用されています。メクトロンは、優れた研究開発と生産技術を活かし、耐久性と精密性に優れた製品を提供しています。製造工程では環境に配慮した方法を採用し、持続可能な事業運営を実現しています。国内外で事業拡大を進め、グローバル市場でも競争力を高めています。
◇ブラザー工業
ブラザー工業株式会社は、プリンターやミシンなどの家庭用製品から産業用機器まで、幅広い製品を製造している総合メーカーです。革新的な技術とデザインを融合させ、消費者や企業の多様なニーズに応えています。環境に配慮したリサイクル素材の使用や省エネ設計を進め、持続可能な社会の実現にも貢献しています。また、積極的にグローバル展開を行い、多くの国で高い評価を受けています。ブラザーの製品は、その品質の高さと使いやすさから、多くの家庭やオフィスで信頼されています。
◇静岡鐵工所
静岡鐵工所は、精密加工機械や産業用設備を製造している老舗企業です。自動車やエネルギー関連部品など、多岐にわたる分野で活躍しており、高い技術力と信頼性が特徴です。長年の経験を活かして、顧客の生産性向上やコスト削減に貢献しています。国内外に広がる販売ネットワークを活用し、タイムリーに高品質な製品を提供し、顧客満足度の向上を目指しています。
◇ニデックオーケーケー
ニデックオーケーケーは、精密加工機や金型製造装置を手掛けるニデックグループの一員で、特に航空宇宙や医療分野向けの高精度な製品を得意としています。最先端技術を活用し、製造現場で高い評価を得ています。顧客のニーズに合わせたカスタマイズ提案を行い、柔軟に対応できる体制を整えています。また、グローバルネットワークを活かし、地域ごとのニーズに応じたサービスを提供し、国際的な信頼を築いています。
◇日精ホンママシナリー
日精ホンママシナリーは、プラスチック成形機を製造する企業で、エネルギー効率が高く、精密な成形技術を持っています。これらの成形機は、家電や自動車部品、医療機器などの製造において重要な役割を果たしています。環境保護を重視した製品開発を行い、地球に優しい製造プロセスを推進しています。また、顧客の多様なニーズに応えるため、技術革新を続け、製品ラインを強化することで競争力を維持しています。
◇オークマ
オークマは、NC旋盤やマシニングセンタなどの精密加工機械を製造している企業で、高い評価を受けています。独自に開発した制御装置「OSP」は、操作性と生産効率を向上させ、製造現場の作業を効率化しています。スマートファクトリー化を支援するため、IoT技術も取り入れており、次世代の製造業の発展に貢献しています。オークマは、国内市場だけでなく、国際市場でも大きな影響力を持ち、高品質な製品と技術革新を通じて、グローバルリーダーとしての地位を確立しています。
難削材は一般的な加工方法では形を変えにくい素材で、航空宇宙や医療機器など高性能分野で重要視されています。これらの材料は耐久性や耐熱性が高く、加工が難しい特性を持っています。
例えば、硬度が高い超耐熱合金やチタン合金、熱伝導率が低い高硬度鋼やコバルト基超耐熱合金、加工硬化性が高いインコネルなどがあります。
これらの材料を効果的に加工するには、適切なマシニングセンタと切削工具の選定が重要です。加工時には、材料の硬度による工具の摩耗や破損、切り屑の溶着や発火のリスクにも注意が必要です。適切な切削条件と工具選びを行うことで、高精度かつ効率的な加工が可能となります。
自社にピッタリなマシニングセンタはどれ?
ニーズで選ぶ! おすすめ企業3選
コスト削減とサポート
メクトロン
個別カスタム得意!
充実のアフターサポートも◎
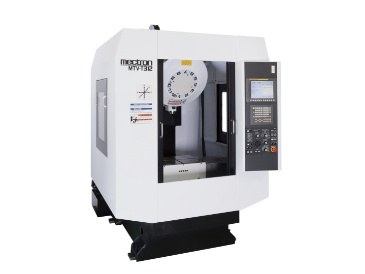
特徴
- ターンキーソリューション対応!設定の手間が省け、失敗のリスクも減らせる
- 自動化システム導入可能!生産性の向上とコスト削減に大貢献
- コンパクトなサイズで設置スペースが限られる工場や作業現場にも適応
品質と耐久性
静岡鐵工所
熟練の技で一台一台を
丹念につくり込む
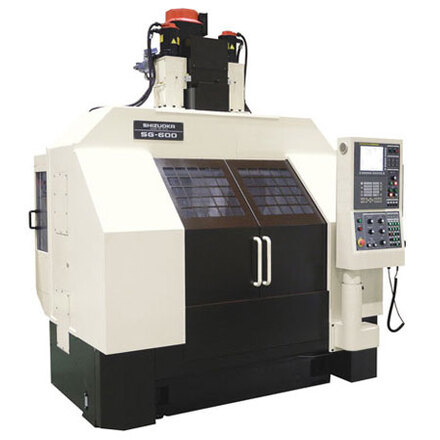
特徴
- 熟練した職人の手で施される、精密かつ耐久性の高い製品
- 強力なギヤヘッドを搭載し、幅広い加工に対応可能

メディア推奨 メーカー6選

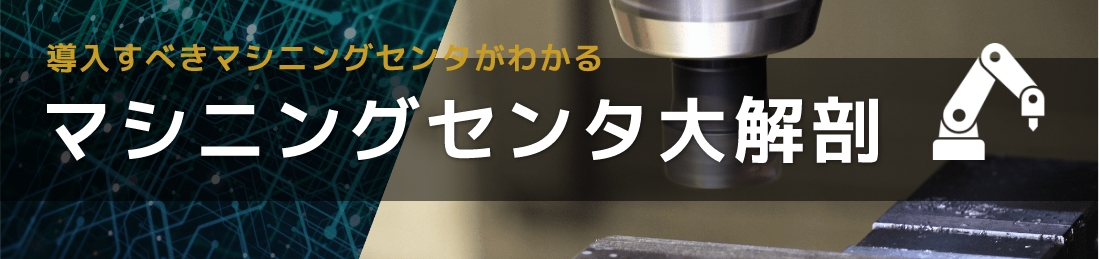