マシニングセンタでよくあるトラブルは?原因とトラブルシューティング | マシニングセンタ大解剖
マシニングセンタの基本
マシニングセンタでよくあるトラブルは?原因とトラブルシューティング
公開:2024.12.17 更新:2024.12.17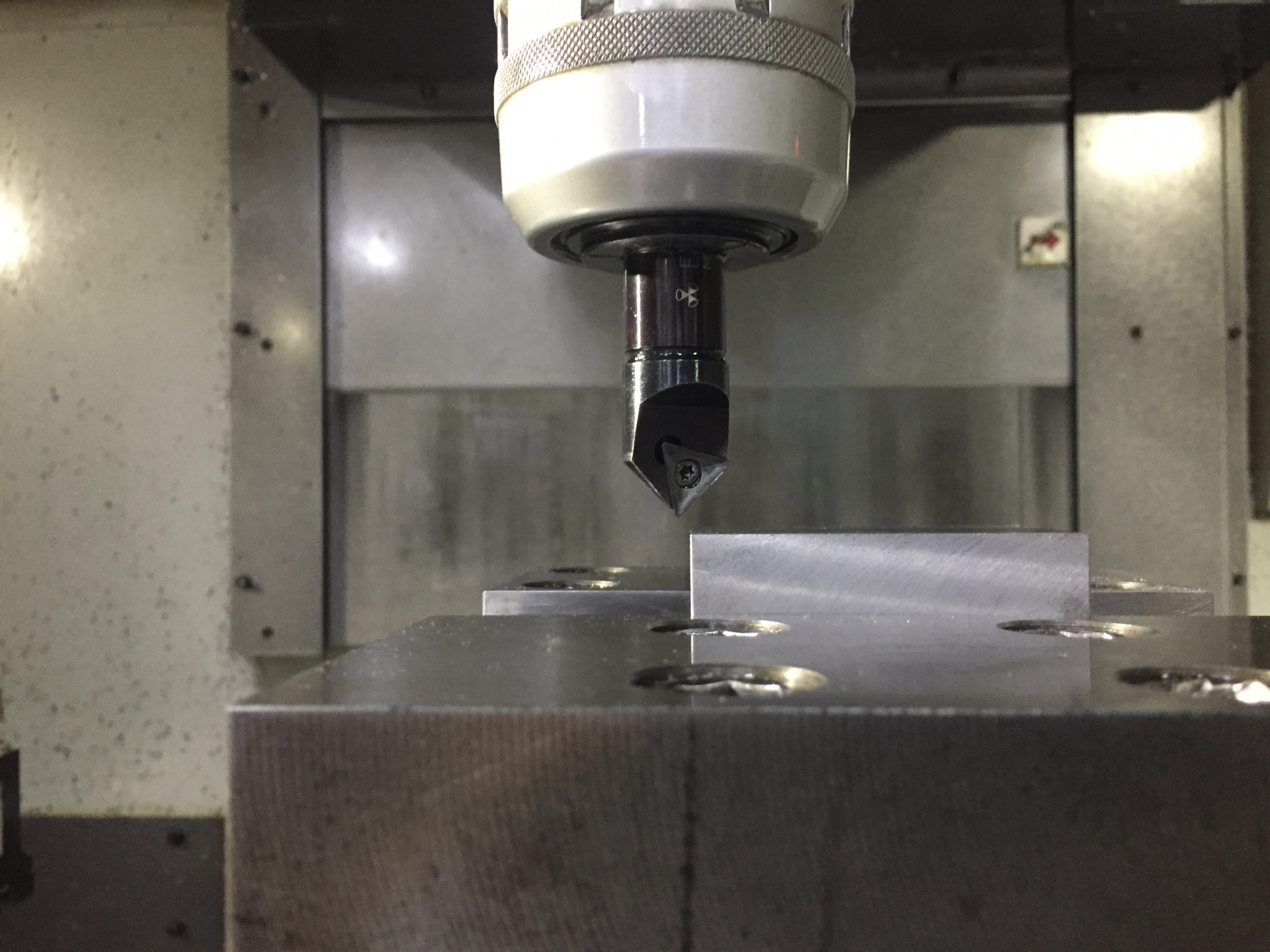
マシニングセンタのトラブルは、生産ラインの効率や製品の品質に大きな影響を与えます。システム障害や人為的ミス、ツールマガジン・ツールチェンジャーの故障など、さまざまな原因が絡み合い、予期せぬ障害が発生することがあります。こちらでは、これらのトラブルの原因と効果的なトラブルシューティング方法について詳しく解説します。
目次
マシニングセンタのトラブルによる影響
マシニングセンタの故障は、生産ラインの停止によるダウンタイム、加工精度低下による不良品発生、納期遅延などの問題を引き起こします。これらは生産効率の低下とコスト増大につながり、企業の競争力に悪影響を及ぼす可能性があります。適切なメンテナンスと予兆保全が重要です。
◇ダウンタイムの発生
マシニングセンタなどの工作機械に故障が発生すると、生産ラインが突然停止し、ダウンタイムが生じます。この停止は加工工程だけでなく、前後の工程や関連設備の稼働にも影響を与えます。特に自動化ラインでは、夜間の無人運転中に発生する故障が深刻な問題となり、大幅な生産性低下と経済的損失をもたらす可能性があります。
復旧には原因の調査や部品の確保が必要となり、場合によってはメーカーの対応も求められるため、計画的な停止と比較して再稼働までに多くの時間を要します。これにより、生産計画の乱れや納期遅延が発生し、企業の信頼性低下にもつながる恐れがあります。
◇不良品が発生
マシニングセンタの故障は加工精度の低下を引き起こし、不良品発生のリスクを高めます3。特に、故障の前兆として精度低下が見られる場合、影響を受けた可能性のある複数ロット分のワークすべてを検査する必要が生じます。これにより、余分な検査時間とコストが発生します。
不良品が確認された場合、製品の廃棄や再加工が必要となり、材料や労力の無駄が生じます。さらに、不良品が顧客に流出してしまうと、企業の信頼性が大きく損なわれる可能性があります。
このような損失を防ぐためには、定期的な点検や機械の状態を常時監視するシステムの導入が重要です。
マシニングセンタでよくあるトラブルとは
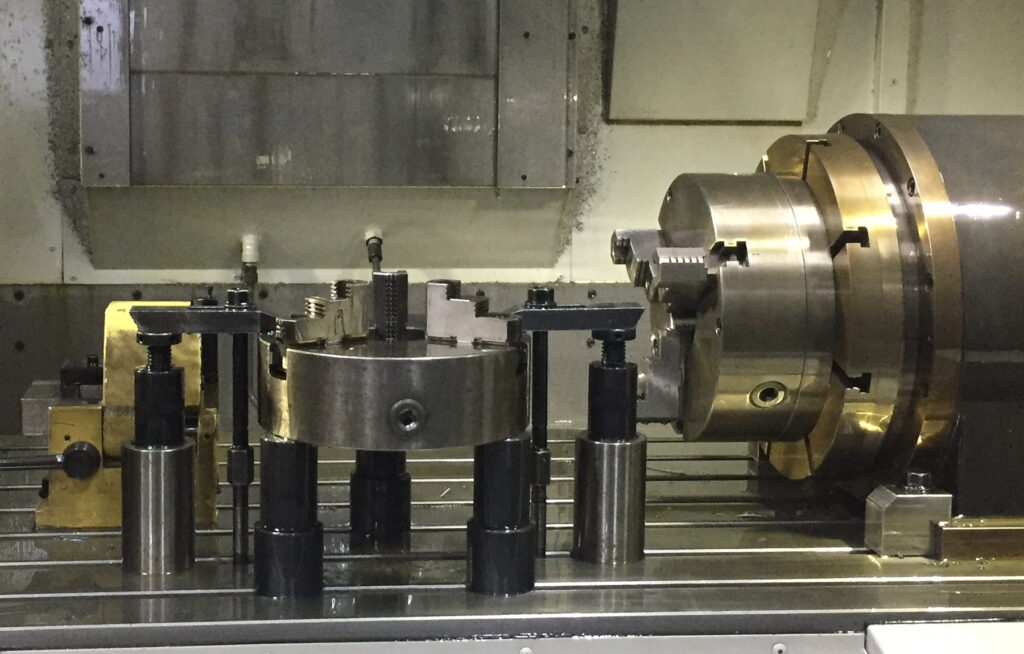
画像出典:フォトAC
マシニングセンタで発生するトラブルは、製造現場の効率や製品の品質に大きな影響を及ぼします。システム故障や人為的ミスなど、多くの要因が絡み合い、時には予期せぬ障害が生じることがあります。
◇システム障害
マシニングセンタで起こりやすいシステム障害は、機械の不調や基準を満たさないコンポーネントが原因となることが多いです。例えば、クーリングシステムに漏れが発生すると、長期間の使用で圧力がかかりやすくなり、動作中の発熱やシステムの応答遅延を引き起こします。
その結果、加工精度が低下し、深刻な場合には警告が発せられ、機械が自動停止することもあるでしょう。また、各軸が指定範囲を超えて移動すると、オーバートラベルアラームが発生することもあります。
◇ツールマガジンの故障
ツールマガジンの故障には、ツールマガジンが正しく回転しない、ツールホルダーが工具を確実にクランプできない、または所定の位置に収まらないといった問題があります。原因としては、モーターシャフトやカップリングの緩み、周波数変換器の故障、低電圧などが考えられます。
また、クランプ力不足は調整ネジやスプリングの緩みが影響することが多く、性能検査や修理が必要です。不適切な調整やリミットスイッチの位置ズレもエラーを引き起こすため、定期的な点検が欠かせません。
◇ツールチェンジャーの故障
ツールチェンジャーの故障は、加工現場で頻発するトラブルのひとつです。例えば、ツールホルダーが工具を締め付けない場合、原因としてクランプ爪のバネ圧不足やスプリングの緩みが考えられます。
また、工具が過大寸法の場合やロック機構の不具合も影響します。一方、工具を緩められない場合は、ルーズロックのバネ圧が強すぎる可能性があるでしょう。さらに、工具交換時に主軸が正確な交換点に戻らず、位置ずれが起きると工具が破損するリスクがあります。
◇人為的なミス
マシニングセンタの運用における人為的なミスは、システム故障と比べるとランダム性が高く、特定の条件下で偶発的に発生することが特徴です。例えば、重要なパラメータ設定や操作手順のミス、接続部品のロック忘れ、リレー接点やスイッチの位置ずれなどが挙げられます。
これらのミスはオペレーターのスキルや注意不足が原因となることが多く、トラブル時に原因を特定するのが難しい場合もあります。
トラブルの主な原因とトラブルシューティング
工作機械の主なトラブル原因としては、メンテナンス不足、ヒューマンエラー、老朽化、偶発的な故障などが挙げられます。それぞれのトラブルに対する具体的な解決方法を理解し、適切な対策を講じることが、機械の安定した稼働を維持するために重要です。
◇トラブルの主な原因
工作機械の代表的な故障原因には、メンテナンス不足、ヒューマンエラー、老朽化、偶発的な故障があります。メンテナンス不足による故障は、定期点検や保守作業が適切に行われない場合に発生しやすく、切粉トラブルなどを引き起こす可能性があります。
ヒューマンエラーは、操作ミスや経験不足が原因となることが多く、主軸の衝突や過度な加工負荷などにつながります。老朽化による故障は、部品の消耗や経年劣化が主な要因で、計画的なメンテナンスが必要不可欠です。偶発的な故障は予測が困難であり、工作機械のライン設計時に考慮する必要があります。
◇トラブルシューティングの基本的な手順
工作機械のトラブルシューティングでは、まず障害の可能性のある原因をリストアップし、それに基づいて一次および二次のトラブルシューティング計画を立てることが基本です。次に、大まかな障害箇所を特定し、メンテナンスを開始します。
具体的には、スピンドルやツールチェンジャーなどの主要部品の故障を考慮します。これらの部品の機械構造や操作方法を理解し、原因を分析することで、適切な修復が可能になります。最終的には、工作機械が正常に動作するよう、総合的な整備を行います。
◇ツールマガジン・ツールチェンジャーのトラブルシューティング
ツールマガジンとツールチェンジャーのトラブルには、共通する問題とその解決方法があります。例えば、ツールマガジンが回転しない場合、モーターシャフトとウォームシャフトのカップリングの緩みが考えられます。この場合、カップリングのネジを締め直す必要があります。
PMC出力がない場合は、I/Oインタフェースボードのリレーの不具合が原因の可能性があり、対応するPMC接点信号の確認が必要です。工具交換の問題では、メカニカルクランプリングの損傷や工具の寸法超過が考えられます。
トラブルシューティングの際は、ツールマガジンやツールチェンジャーのメカニカル接続や電子的な信号処理を重点的にチェックすることが重要です。
生産を止めないためにはメンテナンスが重要
マシニングセンタの安定稼働には定期的なメンテナンスが不可欠です。日常点検や主軸の振れ精度確認により、突発的な故障を防ぎ、生産停止のリスクを軽減できます。
◇日常のメンテナンスや点検
日々の業務に追われると、メンテナンスや点検が後回しになりがちですが、これらを怠ると予期せぬ故障により生産が停止する可能性があります。このような事態を回避するには、日常的な点検が極めて重要です。
各軸のワイパー、エアフィルター、油圧オイルなどを定期的にチェックすることで、突発的な故障のリスクを大幅に低減できます。設備保全の重要性が高まる中、適切な日常点検は安定した生産を維持するための基盤となります。
短時間でも確実に点検を行うことで、長期的には生産性の向上と設備の長寿命化につながります。また、点検作業を通じて機械の状態を把握することで、オペレーターの機械に対する理解も深まり、より効率的な運用が可能になります。
◇主軸の振れ精度の確認
主軸の振れ精度を確認することは、マシニングセンタ全体の状態を把握する上で非常に重要です。マシニングセンタの駆動部の中で、主軸は最も酷使されるユニットであり、その精度は劣化の影響を受けやすいです。
主軸の振れが大きくなっている場合、駆動系を中心とする構成部品の消耗や経年劣化が進行していると判断できます。テストバーを使用して主軸の振れ精度を確認することで、簡単かつ短時間で主軸の状態を評価することができます。
この方法は、低コストで実施可能な予知保全の一つとして有効です。定期的に主軸の振れ精度をチェックし、その推移を記録することで、将来的な故障や精度低下を予測し、計画的なメンテナンスや部品交換を行うことが可能になります。これにより、突発的な生産停止を防ぎ、安定した稼働を維持することができます。
マシニングセンタの故障は、ダウンタイム、生産効率の低下、不良品の発生、納期遅延など、多くの問題を引き起こします。これにより、企業の競争力が大幅に損なわれる可能性があります。適切なメンテナンスと予兆保全が重要であり、日常的な点検や主軸の振れ精度の確認が欠かせません。
マシニングセンタの故障を未然に防ぐためには、システム障害や人為的ミス、ツールマガジン・ツールチェンジャーの故障など、さまざまな原因を理解し、それに対する対策を講じることが必要です。
予測可能な故障を防ぎ、生産ラインの安定稼働を確保するためには、計画的なメンテナンスと常時監視体制の導入が不可欠です。これにより、企業の信頼性を維持し、コストの増大を防ぎます。
自社にピッタリなマシニングセンタはどれ?
ニーズで選ぶ! おすすめ企業3選
コスト削減とサポート
メクトロン
個別カスタム得意!
充実のアフターサポートも◎
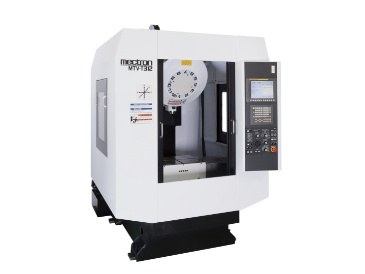
特徴
- ターンキーソリューション対応!設定の手間が省け、失敗のリスクも減らせる
- 自動化システム導入可能!生産性の向上とコスト削減に大貢献
- コンパクトなサイズで設置スペースが限られる工場や作業現場にも適応
品質と耐久性
静岡鐵工所
熟練の技で一台一台を
丹念につくり込む
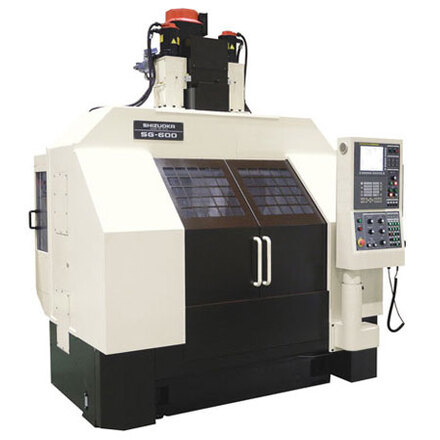
特徴
- 熟練した職人の手で施される、精密かつ耐久性の高い製品
- 強力なギヤヘッドを搭載し、幅広い加工に対応可能

メディア推奨 メーカー6選

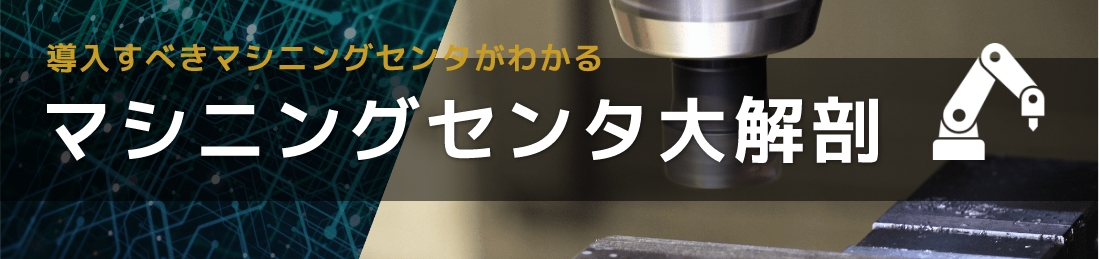